
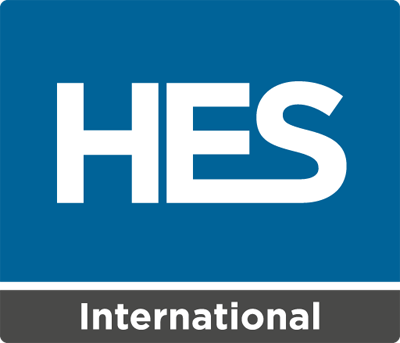
HES Gdynia
IBM Maximo proves a real asset for HES Gdynia
Implementation of a new Enterprise Asset Management System provides improved visibility of critical information, allowing the client to optimize its decision-making and improve its work effectiveness.
Summary
Cohesive’s expert team implements IBM Maximo as a new Enterprise Asset Management System for HES Gdynia, one of the biggest seaports in Poland, providing improved visibility of critical information, allowing the client to optimize its decision-making and improve its work effectiveness.
Solutions

The Challenge
HES Gdynia Bulk Terminal is a part of HES International, one of Europe’s largest independent terminal operators in dry and liquid bulk products. HES terminals operate in Europe’s most important ports at prime locations, including a bulk cargo terminal in Gdynia, one of the biggest seaports in Poland.
HES Gdynia acts as a universal terminal providing 24-hour transhipment services and storage of dry bulk cargoes such as coal, coke, and ore and uses a modern and diversified fleet of assets, including grab hook cranes, hoppers, wheel loaders, rolling equipment, rail- and truck weighbridges.
HES wanted to implement an asset management system (AMS) to manage and maintain cranes, loaders and other equipment. Its primary objective was to significantly improve the efficiency of maintenance work.
HES also wanted to eliminate paper versions of its work and repair reports and to build a central repository of all information about its assets. The goals were defined as follows:
- Building a central database of assets to collect all required information within the electronic repository
- Providing support for processes in the planning and realization of maintenance works following HES internal procedures and external regulations
- Failures registration, along with analysis and handling
- Development of a mobile application to support maintenance works in the field and registration of all undesirable events including failures
- Optimization of human resources management along with the necessary supervision regarding permissions and qualifications to perform tasks
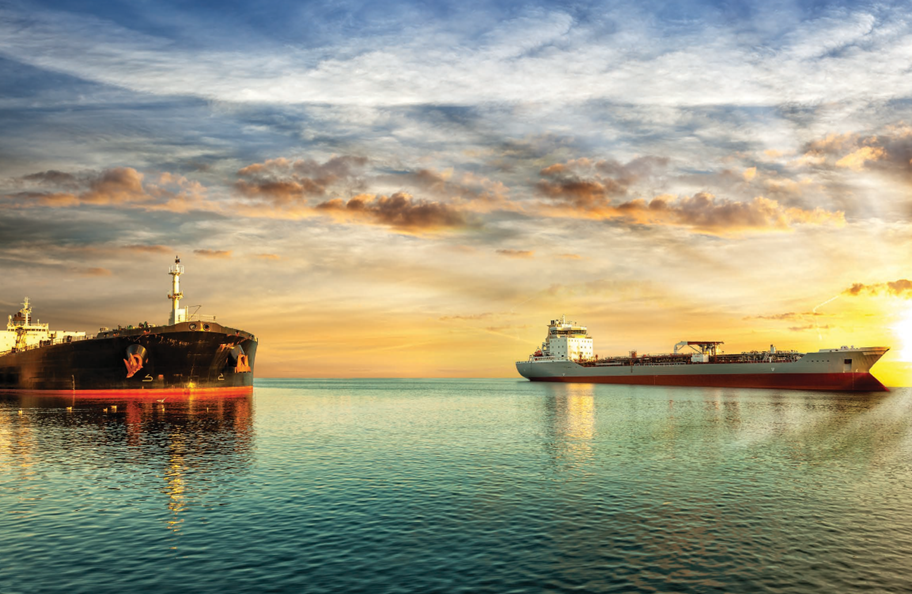
Our Solution
The delivered solution was based on IBM Maximo Asset Management 7.6 with a custom mobile application; and Cohesive’s Maximo knowledge and industry, organisational and technical skills helped to ensure an efficient implementation of the system.
The specific modules of IBM Maximo Asset Management implemented were:
- Asset Management
- Warranty
- Asset Meters
- Contracts
- Inventory
- Job Plans
- Preventive Maintenance
- Work orders
- Service Request
- Crafts and Competencies
With the mobile application supporting failure reporting and work orders.
All of the existing data was migrated from Excel files and was prepared in line with data in legacy systems.
In some cases, data was derived directly from technical documentation and Cohesive was further responsible for preparing detailed design and technical documentation of the solution.
The implemented solution covered the following areas:
- Asset repository with classifications, attributes, and relationships, as well as records of asset ownership agreements and guarantees
- Tracking downtime of assets due to maintenance or breakdowns
- Each asset’s meter management
- Inventory management regarding tools and materials necessary to complete work orders
- Planning processes (daily, mid-, and long- term preventive maintenance) with the alignment to internal HES procedures and external regulations
- Job plans and automatic work order scheduling (calendar and meter-based)
- Work orders management (planning, assignments, realization, reporting)
- Staff management required for maintenance tasks including skills, competencies, and shifts
- Alerting via SMS and mobile application – work assignments, failures, escalations
- Handling processes related to failures and breakdowns: the registration, failure analysis, and work orders to compensate for the effects of undesirable situations and repair
- Support for decommissioning processes
- Development of a mobile application for failure reporting and work orders (assignments, reporting)
- Custom reports for assets and work orders analysis
The Client Benefits
The implementation of IBM Maximo Asset Management with the added mobile solution has delivered many benefits to HES, including:
- The ability to track, manage and maintain significant assets
- Real-time access to resources and work order information
- Automation of business processes in the field of improving records and management of assets
- Access to the history of works and the life cycle of assets
- Improving the management of maintenance works and repairs
- Reducing the time from failure reporting (with the use of the mobile app) to repair
Further development work is also ongoing, especially regarding extending the functionality of the mobile application.