
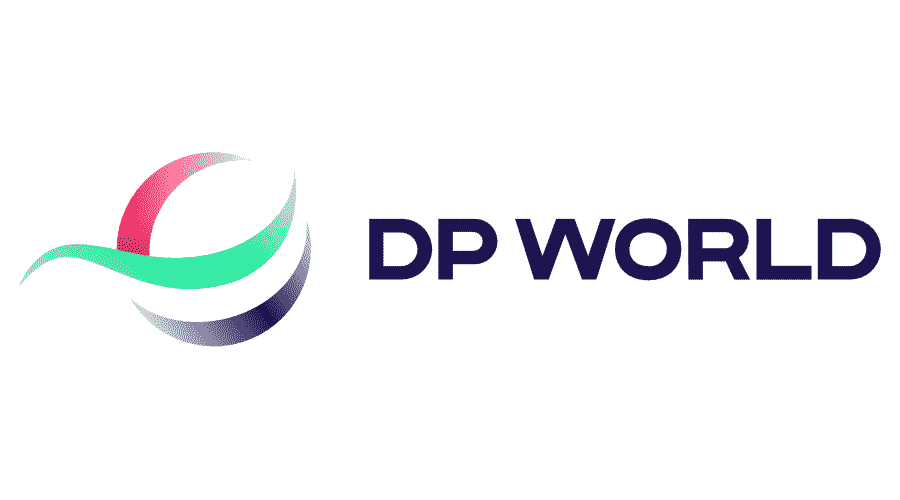
DP World
Preventative maintenance with IBM Maximo allows smarter asset management for DP World
IBM Maximo helps DP World move away from a ‘break-fix’ maintenance model and towards a more proactive, preventive approach. As a result, the company is performing 10% more preventative maintenance and suffering 10% fewer actual breakdowns.
Summary
IBM Maximo implemented by Cohesive helps DP World move away from a ‘break-fix’ maintenance model to a more proactive, preventive approach by enabling engineering technicians to interact directly with the new system to review the complete service history of each piece of equipment that is being maintained, helping them diagnose potential problems and schedule remedial maintenance work, resolving issues before they occur. The company now performs 10% more preventative maintenance and suffers 10% fewer actual breakdowns.
Solutions

The Challenge
DP World Southampton is the second-largest container terminal in the UK. Founded in 1985, it spreads over 200 acres (81,000 sq m) and contains four deepwater berths, one short-sea berth, 14 ship-to-shore gantry cranes, one mobile harbor crane, and over 100 straddle carriers to load and unload the containers to and from ships and onto trucks and trains. Two large workshops handle maintenance for these crucial assets. The terminal employs over 780 people and has an annual capacity of over two million TEU (Twenty-Foot Equivalent Units).
“The containers we process bring cargo from all over the world and can hold anything from expensive consumer goods to frozen foods or hazardous chemicals, so we need to be able to store each shipment appropriately, securely, and safely, as well as ensuring that it is loaded for delivery on time. To meet all these demands, we need to manage and maintain thousands of different assets, from the largest super post-Panamax gantry cranes down to the spare parts required by berth vehicles,” says David Bowers, Engineering Planning and Quality Manager, at DP World Southampton.
Equipment breakdowns can cause massive problems, delaying goods in transit and incurring heavy maintenance and repair costs, so the company wanted to find a way to improve maintenance performance, increase efficiency and reduce operating costs.
A legacy computerized maintenance management system (CMMS) was not well adapted to the company’s business processes and as a result, it was difficult to manage the maintenance workload intelligently and to ensure that equipment was serviced often enough to meet ISO 9001:2000 quality standards and to comply with health and safety regulations.
David Bowers again: “We found that 80% of our maintenance work was aimed at fixing breakdowns, rather than preventing them. Every time a crane breaks down, it slows our throughput and ultimately costs us money. We realized that if we could find a way to be more proactive in our maintenance work, we could keep the terminal fully operational for longer periods, reducing delays and boosting efficiencies.”
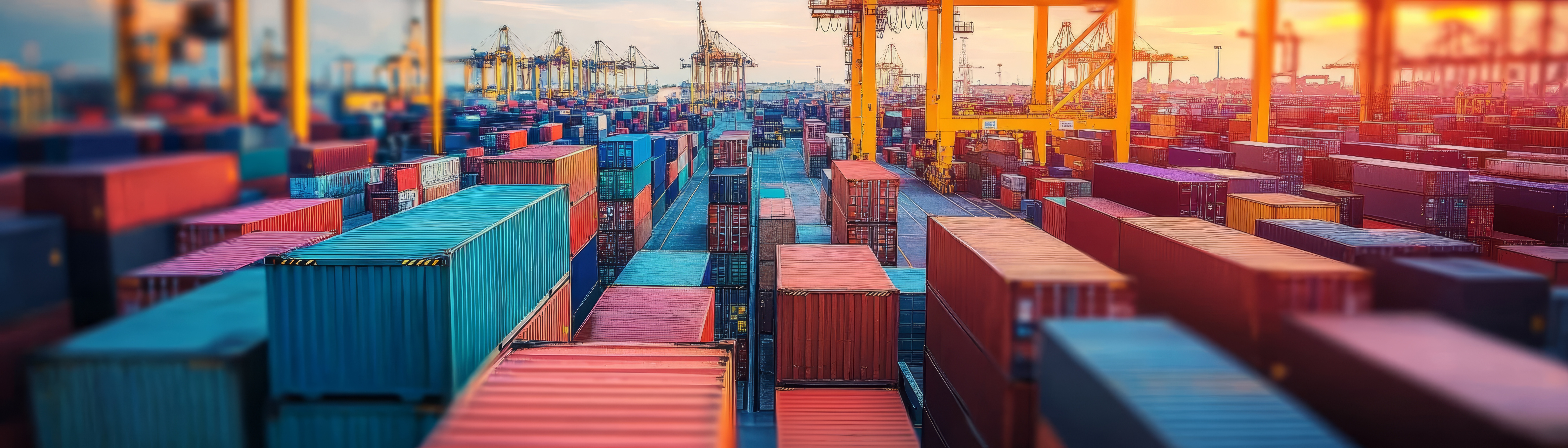
Our Solution
A dedicated maintenance team was tasked to oversee the implementation and ongoing optimization of a new CMMS to align it more closely with the unique operational needs of the business.
IBM Maximo Asset Management was one of the few products on the market flexible enough to meet all DP World’s requirements and Cohesive was recommended as the partner of choice by the IBM team.
The Cohesive team’s experience of working with marine engineering and shipping companies, and deep understanding of the types of challenges DP World was facing, ensured that optimal, best practice solutions were implemented.
Broader access to technology
Ensuring access to the CMMS data for the engineering technicians in the terminal’s workshops provides a wealth of useful information that helps them to diagnose potential problems before they occur and move from a ‘break-fix’ maintenance model towards a more preventative approach.
David Bowers explains: “As an example, here’s a common scenario; one of our straddle carriers comes in for unscheduled maintenance after a breakdown. The engineering technicians rectify the problem but notice an additional defect that will need attention in the future. Rather than feedback verbally, the Engineering Technicians can now raise remedial work orders in Maximo to report the defects. Then supervisors review the feedback, prioritize and schedule the work to be completed as soon as possible or when the next planned maintenance is carried out.”
Matching IT to business processes
Cohesive worked closely with the in-house team to analyze the company’s maintenance, finance, procurement, inventory, and logistics processes. The next step was to create documentation and then deploy and configure the Maximo Asset Management software.
Maximo has been set up to help manage both the maintenance processes and associated processes like procurement and inventory management for spare parts and equipment. Spare parts in the stores are barcoded and scanned directly into the system, so DP World Southampton can see when supplies are running low and need to be reordered.
The Client Benefits
The preventative maintenance approach eliminated breakdowns, so the straddle carrier is fully operational until the next planned maintenance session. Engineering technicians are equipped with the tools they need to record, plan, and fix problems before they happen.
- De-risking the human error possibility – engineering technicians now log their maintenance reports directly into the system as they work.
- Instant information – the contractors’ servicing and maintenance record updates capability gives a full overview of all assets.
- Enhanced traceability helps with audits, inspections, and regulatory compliance.
- Improved workflow and inventory management ensure that the right parts are used for the right jobs.
Further business benefits
- Engineering technicians can diagnose problems more effectively and take preventative measures to help prevent breakdowns.
- The company is performing 10% more preventative maintenance and suffering 10% fewer actual breakdowns.
- Workflow-based process management helps enable tighter control of maintenance scheduling and costs.
- Full traceability and advanced reporting functions help simplify regulatory compliance.